Integrated Design-Build: Why It’s Better, Faster and More Cost-Effective
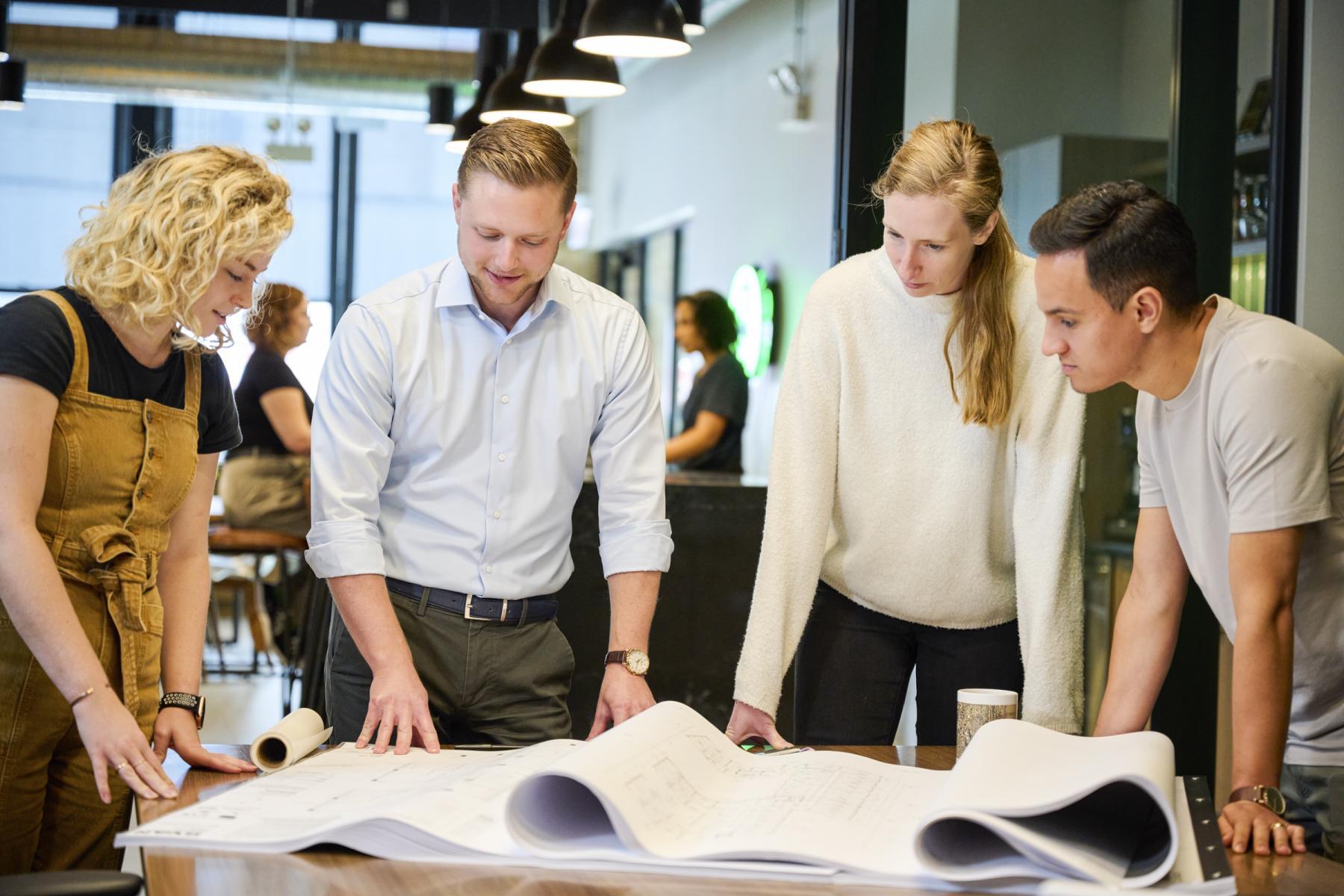
An integrated design-build approach can help facilitate a seamless process for your next project, thanks to transparent communication and multiple experts at the same table.
With approachability and clarity at its core, this type of approach to designing and building facilities can lead to quicker decisions, more effective options and a better, faster and cheaper result.
In an integrated design-build approach, teams within the same company offer their expertise and diverse points of view. Teams collaboratively communicate by simply walking down the hall or gathering in a conference room. Effective solutions are identified quicker, and challenges are solved more seamlessly before they become barriers.
For this to be successful, it starts and ends with open communication. Just ask Whit Noxon, our associate director of architecture.
When Whit begins working with her team on the design of a new project, she asks one question:
How can I make this better for the person sitting across from me?
She considers multiple points of view—from the client to the construction team to the procurement team to the end user— to gain a well-rounded view and determine the best design options.
Read on to learn from our design team and the reasons why an integrated design-build process can save you time and money while achieving your project goals.
CAPTURED LESSONS, CONTINUOUS IMPROVEMENT
Because our teams can maintain a seamless flow of communication, an integrated-design approach helps our team members capture lessons learned to continuously improve processes.
Our design, construction and field teams own the process and are encouraged to say, “This isn’t working. Let’s do it differently.” After each project, our design team captures and communicates valuable feedback from our construction team by asking questions, including:
- Did you have a challenge with the product?
- Did the product reps offer support in the field?
- Did this product include quality installation guides?
Sometimes products do not translate into exceptional customer service or a quality installation experience for our construction team. Thanks to the feedback loop, our design team can know about the experience to select a better route the next time.
As an example, our design team identified significant issues that our construction team faced when selecting shower pan options on a series of multifamily and senior living projects in Minnesota. Shower pans (manufactured fiberglass extruded components of a shower floor) help prevent water from seeping into the floor. The way the pans were constructed made it impossible for the construction team to build a shower with the appropriate space adjacent as required by the accessibility code.
Our designers started calling around for unique molds, explaining to manufacturers the challenges of finding a compliant pan and why their pan didn't allow for a compliant assembly. As the message continued to spread to manufacturers, more viable options became available while former, noncompliant products were getting removed from websites.
By communicating with our construction team and taking steps to identify the shower pan issues, our design team was able to help improve the process, solve the problem effectively and educate manufacturers, which improved the quality and usability of available product options.
MULTIPLE PERSPECTIVES, STRATEGIC SOLUTIONS
The most strategic design decisions are ones that consider multiple perspectives. When team members are all under the same umbrella, it’s easier to hear each team’s concerns, challenges and preferences. Considering numerous vantage points early in the process can lead to strategic choices that minimize risk and complication down the road.
Clarendale Six Corners, an upscale senior living project in Chicago benefited from the integrated perspectives of the design and construction team.
The designers needed an option that would simplify the labor of installing the shower—a high risk area in buildings for growing mold—without compromising on aesthetics. The team worked with Ryan’s procurement partners to identify a panel system that looked like tile, installed easily, reduced mold growth and did not require immense effort to clean. Our design team tested various tile panels that eliminated grout, but also consulted with our construction team and other key players involved to understand the nuances of each option.
The result? A tile look that met the market demands, longevity desires of ownership, and simplicity in construction and maintenance.
EASIER ACCESSIBILITY, CLEARER COMMUNICATION
The beauty of an integrated design-build process is everyone is sitting at the same table – figuratively and literally.
At Ryan, our construction and design teams can have candid, open conversations. Construction can come to our design team with sequencing, delivery and site layout challenges with lead times long before our design team has issued documents.
Similarly, our architects can sit down with a mason and have conversations about brick layout and pattern. Rather than guessing, our team can say, “This is what I’m thinking for an idea…what would you want, what would make your job easier, what would you want to do?”
This transparent flow of communication can contribute to identifying the best solution, along with preventing pain points.
For example, Eleven—the tallest residential tower in the Midwest— is a gem of the Minneapolis skyline and a symbol of multifamily luxury. Our A+E team built a mockup unit of Eleven to test design and construction of the project, including the windows at the patios.
The original design intent was to utilize windows with a 18" wall below: leveraging less costly construction materials and aligning with all the other windows in the space. But when we built the mockup, the short wall was complicated, fussy and time consuming-to build.
Thanks to helpful discussion with the project’s superintendent, being present on the site and listening to the tradesmen who were doing the work, the team determined it was better to eliminate the short wall at the patio. This decision resulted in windows that ran down to the floor and made the patios feel like an extension to the living room—a pleasing and attractive aesthetic—while saving the project over $100,000 in cost, primarily from decreased labor.
Through our real-life testing, our team was able to identify a design improvement with the patio windows that would improve constructability, enhance the resident experience and save money.
Communication and transparency—and a team of experts all under one roof—truly elevates the design-build process, which translates to time saved and strategic solutions identified early in the process. With continuous communication and easy accessibility to multiple experts, our team provides the best solutions for all involved.
With nearly 20 years in the architecture industry, Whit Noxon, AIA, Ryan’s Associate Director of Architecture – Multifamily, believes that high-quality design work goes above and beyond a beautiful buildings to include excellence in purposeful programming, a deep understanding of constructability and sequencing, detailed coordination with preconstruction partners for budget alignment and intentionally thoughtful space planning.
CONNECT WITH US
Learn more about our integrated design-build process and our design capabilities.
Mike Mahoney
President of West Region
California - San Diego 858-812-7958 mike.mahoney@ryancompanies.com- Email: ryan.pr@ryancompanies.com
- Phone: 612-492-4160