3 Questions to Ask Before Constructing a Food & Beverage Facility
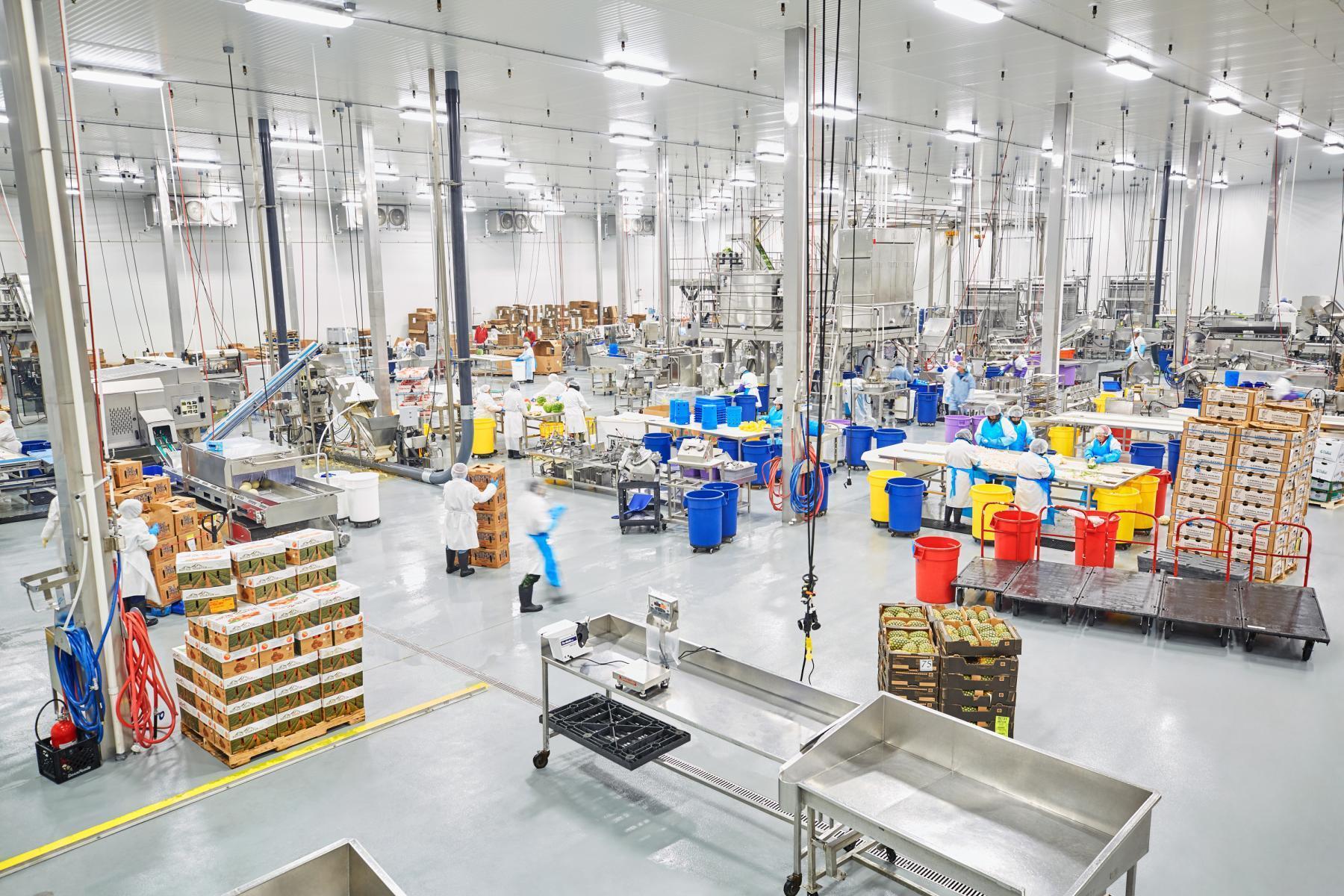
When food and beverage companies decide it’s time to update or construct a new facility, they often want that facility to help improve and streamline their overall production process.
Because of this, the building itself could be viewed as secondary in importance. The entire purpose of the facility, after all, is to support successful and safe production.
But it takes participation by all key players, including experts in real estate, process engineering, process building, mechanical engineering and design, as well as robust project management teams, procurement teams and execution teams, to ensure a comprehensive understanding of the production process. Creating a sense of understanding can result in a successful facility that meets needs and goals while improving efficiencies and ROI.
So what helps pave the path to success? Asking (and answering) the right questions before a shovel even hits the ground.
Here are three questions—as defined by our industrial food and beverage experts here at Ryan Companies—that create that necessary sense of understanding amongst all entities involved, and help ensure a more efficient and goal-aligned project while saving time and money.
QUESTION 1: Who will support the project?
As a food and beverage company moving forward with the construction of a new facility, you have two options: hire a team internally or partner with an external company. In hiring an internal team, you need to ensure team members understand the food and beverage side of how the plant operates, the facility side of the process and what will work best to design and construct your facility.
The second option is to hire an external company that can do the heavy lifting for you and meet you where you are, providing a team of experts to examine all facets of the project—including the real estate component.
But not many groups offer full-service turnkey from real estate to technical execution to Startup and Commissioning. Because our experts offer a complete team under one roof, our process is streamlined and creates a smoother communication flow with fewer hurdles for clients to navigate, and in turn, creates faster speed to market.
Our expertise across numerous aspects of the process allows everyone to be present at the table, providing each client with a one-stop shop approach. From the start to the end of the project we collaborate with your project team to identify what is needed to make the project happen and gain project approval.
QUESTION 2: What type of facility is needed?
Projects evolve, which is why it is important to gain a comprehensive understanding of the site in the beginning stages, including:
- Is it an existing facility?
- A new facility?
- What are the tenant and lease agreements?
You need to know where you are putting a project and what type of building you need. Otherwise, you risk playing a guessing game and end up with redesign efforts or incorrect sizing, which adds time and cost. Harnessing the power of our real estate management team and Ryan Building Services team can help streamline the process from the get-go, allowing you to visualize an accurate picture of facility needs.
Once our real estate team is engaged, the next most important group is the process design team. Because there are numerous equipment components involved, each piece of equipment must be installed in a certain order and configuration. Until that configuration and that general arrangement is understood, you cannot begin design. It is imperative to design a building that fits around your process.
QUESTION 3: How can the design and construction process ensure proper safety regulations are followed?
Safety is prioritized upfront to avoid causing unintentional harm or illness to consumers. Therefore, equipment layout and equipment size must also be prioritized when considering design factors to maintain safety standards.
When we are involved in this part of this process at Ryan, our architecture + engineering team can look at this process from a strategic lens. For example, our team can critically think, “How can we meet the safety process requirements to ensure this food item is safe to consume?” Along with the food item itself, the building environment needs to be safe as well, which often means the incorporation of wash-down and hygiene areas into the design.
To do so, our experts collaborate with process engineers to create a plan. Next, our construction team can come in and say, “We understand how you are implementing safety with your process; now let’s build the building safely. Let’s utilize food-safe design to help prevent unnecessary contamination.” Together, the team can identify all critical components of safety, making decisions before acting on those decisions to ensure everyone is on the same page to achieve an effective design.
Within each food and beverage facility, preplanning is a game changer. The planning of what you want to do and how much you want to spend—then getting the plan in on paper— helps support a streamlined process and accomplish cost savings.
As part of the preplanning process, our Ryan team can serve as a one-stop shop for clients to funnel all questions and receive answers, making response and design times more efficient and effective.
With intentional preplanning and collaboration with a team of experts that considers every angle of the process, you can help set yourself up for success and save money and time.
CONNECT WITH US
Contact Scott to discuss the next steps for your food & beverage manufacturing project