Bringing Kroger's Vision to Life: 3 Ways Ryan Helped Integrate Grocery Fulfillment Centers' Automation
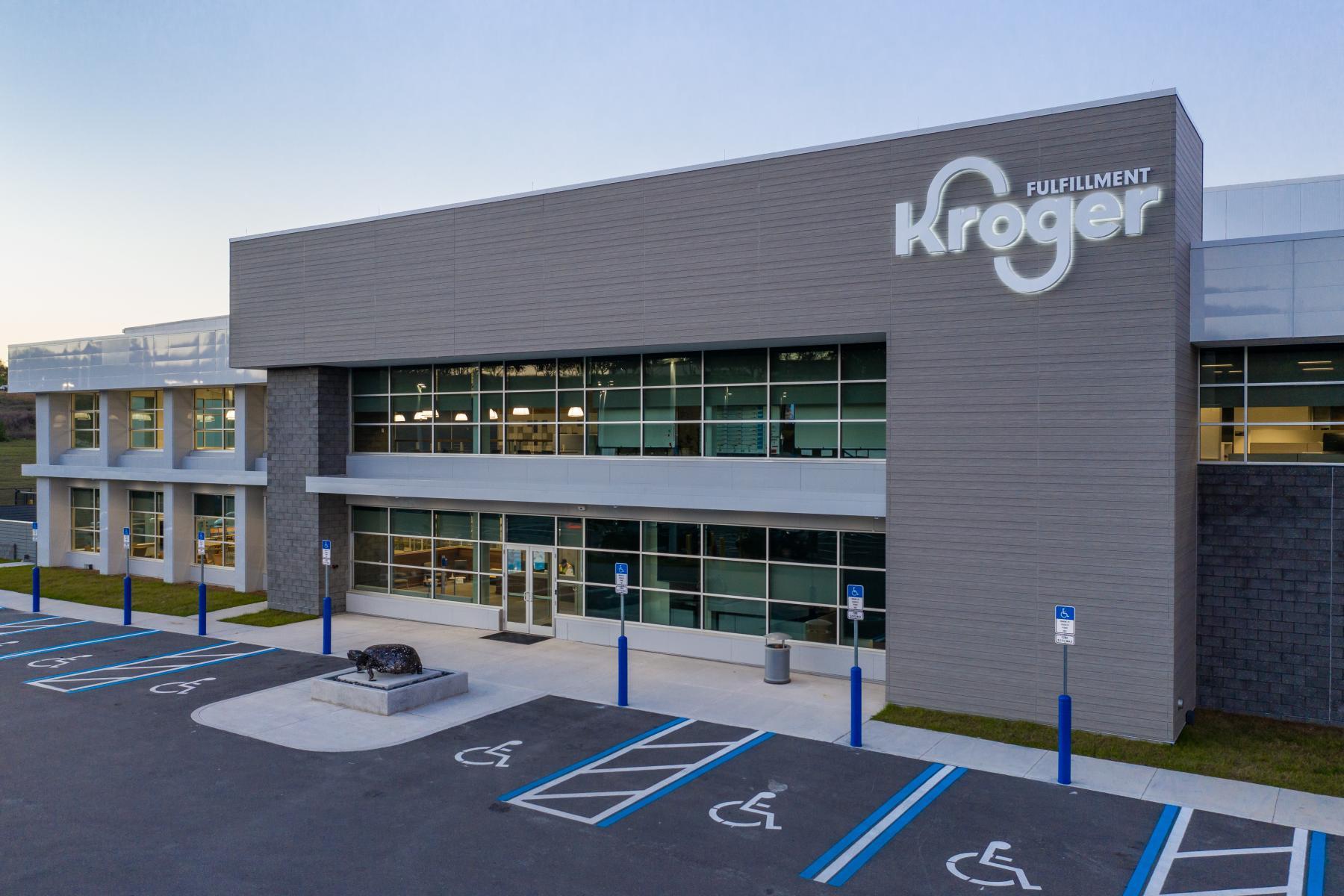
When Kroger set out to build the first comprehensive, automated grocery fulfillment centers in the U.S., one of their key tasks was to build the sheds and frameworks to house Ocado’s sophisticated automation. The automated system, created by Ocado Group in the U.K., features hundreds of robots that operate on a grid called “The Hive,” working quickly and accurately to fill thousands of online grocery orders daily with the help of Kroger associates. Creating a new framework to merge the best of Kroger’s existing fulfillment centers with an advanced automation solution was key. Kroger turned to us for help and insight.
Now, several years later, we are the designer and builder for the Kroger sheds that house Ocado automated fulfillment technology, creating six of the current live facilities, with plans for more. Here are three ways our team has helped Kroger translate their vision into these innovative, automated distribution centers:
1. Define their vision.
One of our first tasks was to define their vision and standards for these automated fulfillment centers. Working closely with Kroger, we narrowed which standards from their traditional distribution centers applied to the automated facilities and rightsized the scale to better meet evolving space needs and fulfillment goals. Evaluating each location individually, we worked out the site-specific details and gave Kroger confidence moving forward as they expanded into new locations. Our integrated design-build services and more than 80 years of complex industrial project experience allowed us to recommend solutions and stay flexible as multiple locations were designed in tandem. Kroger’s needs and goals have evolved throughout the program, and we’ve consistently brought forward solutions to meet their needs.
“Ryan Companies approached every situation as a true partner – recommending thoughtful solutions and explaining the impact of each solution without overburdening Kroger on the behind-the-scenes efforts,” said Matt Theiss, a project manager in facility engineering at Kroger.
2. Partner with both Kroger and Ocado.
Ryan served as project anchor, fostering seamless integration between Kroger (owner), Ocado Group who install and operate their automated solutions within the sites, and our own design-build team. Developing a strong partnership with both Kroger and Ocado was essential to providing coordinated delivery and consistent outcomes. Partnering with Ocado as the automation provider and operator allowed Kroger to receive a custom solution for their vision of continuing as leaders in the grocery delivery market. Using our past automation experience and insight, we were able to increase efficiency, reduce costs and streamline the delivery timeline from 24 to 14 months. Both companies benefited from our support with aspects of the build requiring specific geographical knowledge including fire suppression systems, building code expectations, etc., all while educating teams on the critical technical aspects to help successfully deliver the first automated fulfillment center in partnership between Kroger and Ocado.
3. Maintain open communication and ask the right questions.
Integrating Ocado’s automation required clear communication and the ability to anticipate challenges and provide solutions. Our pulse on the rapidly changing industry and complex industrial experience enabled our teams to ask the right questions and stay on top of changes. Weekly collaboration meetings helped us meet all of Kroger and Ocado’s requirements, and we often used 3-D and 4-D modeling as a communication tool to help everyone understand the vision and the integration. The team worked successfully with some of Ocado’s overseas teams, whilst COVID-19 travel restrictions remained in place. We defined ways to best share files, stay on the same page and support their team members.
Kroger continues to rely on us for our national industrial footprint, local expertise and collective insight—especially as it pertains to integrating fulfillment technology. We define our success based on their success and Kroger knows our teams will reach far beyond traditional expectations to provide whatever is necessary to make these projects thrive.